精緻な抜きの技術
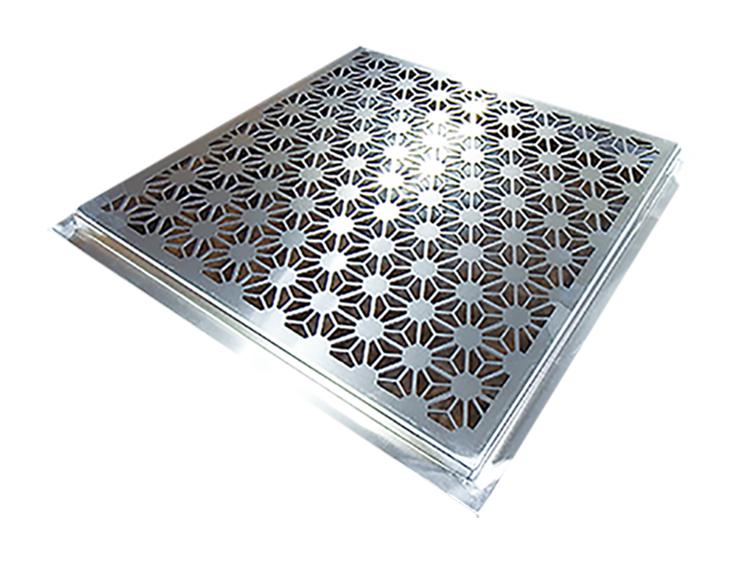
材質 | アルミ (t=2) |
板厚 | t=2 |
サイズ | 400 × 400 (mm) |
アルミで製作した門扉の加工事例をご紹介します。
この製品の特徴は、「ひずみやすいアルミ」に「精巧なデザインを忠実に再現したこと」です。
第一に、アルミのひずみやすさです。
アルミは鉄やステンレスに比べて、ひずみやすいという特徴があり、単純に端から抜いていくと大きなひずみが発生してしまいます。
どこからどのようなルートで切断するとひずみを抑えられるか、を幾度もの試作を経て、最適解を見つけ出しました。
第二に、精巧なデザインの再現です。
サイズが大きく、なおかつデザインが複雑なため、この製品の加工プログラムのデータは非常に膨大なものでした。
そのため、通常通りのプログラムでこのデータを読み込ませると、機械がメモリ不足となって停止してしまいます。
機械が停止する問題を回避するために、エンジニアが加工プログラムに何度も修正を重ねることで、2個目の難点を乗り越えました。
最後に、仕上げとして、
これらの過程で発生する僅かな歪みを、職人の精緻なプレス工程によって極限まで修正して、この製品を完成させることができました。
今回のような、加工難易度が高い製品にも、ヤマダの技術力でお客様のご要望にお応えしております。
できないと思われる形状でお困りの際にも、まずはお問合せください。
最新機を使ったパイプの抜きの技術
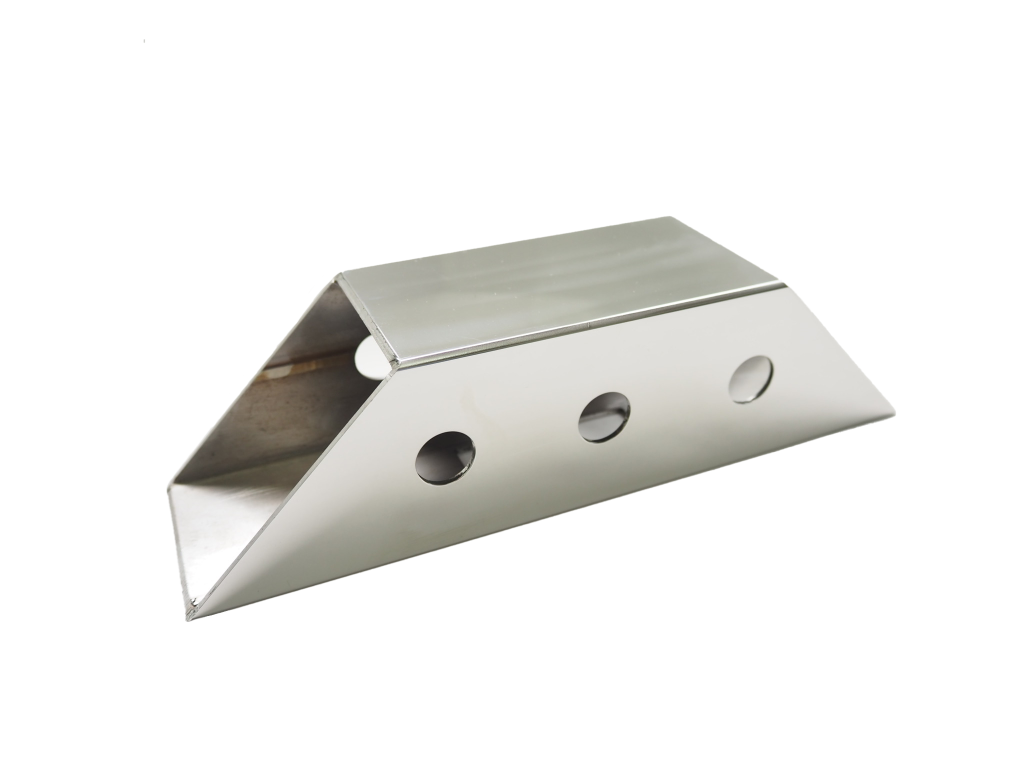
材質 | SUS304 (ステンレス) |
板厚 | t=2 |
サイズ | 60 × 60 × 230 (mm) |
鉄パイプの加工事例をご紹介します。
この特徴は、「パイプのベベル切断」に対応できることです。
べベル切断は、切断加工における方法の一種で、切断した面が斜め(べベル)の角度をもつように切断する方法です。
ベベル切断ではない従来の切断方法でパーツを組み合わせると、溶接面積が大きくなり、溶接・仕上げの工数が増えてしまうという課題がありました。
ヤマダは積極的な設備投資を進める中で、45°のベベル切断に対応可能なトルンプ社製「TruLaser Tube 5000 fiber」を導入しました。
これにより、パーツを組み立てて垂直を出す際に、45°に切断した2本のパイプを組み合わせることができるようになりました。
結果として、溶接面積が小さくなり、コスト・納期短縮に繋がり、また溶接面を視覚的にも美しく仕上げることができるようになりました。
板金はもちろん、パイプの加工もヤマダにお任せください。
送り曲げ(FR加工)による複雑なR形状技術
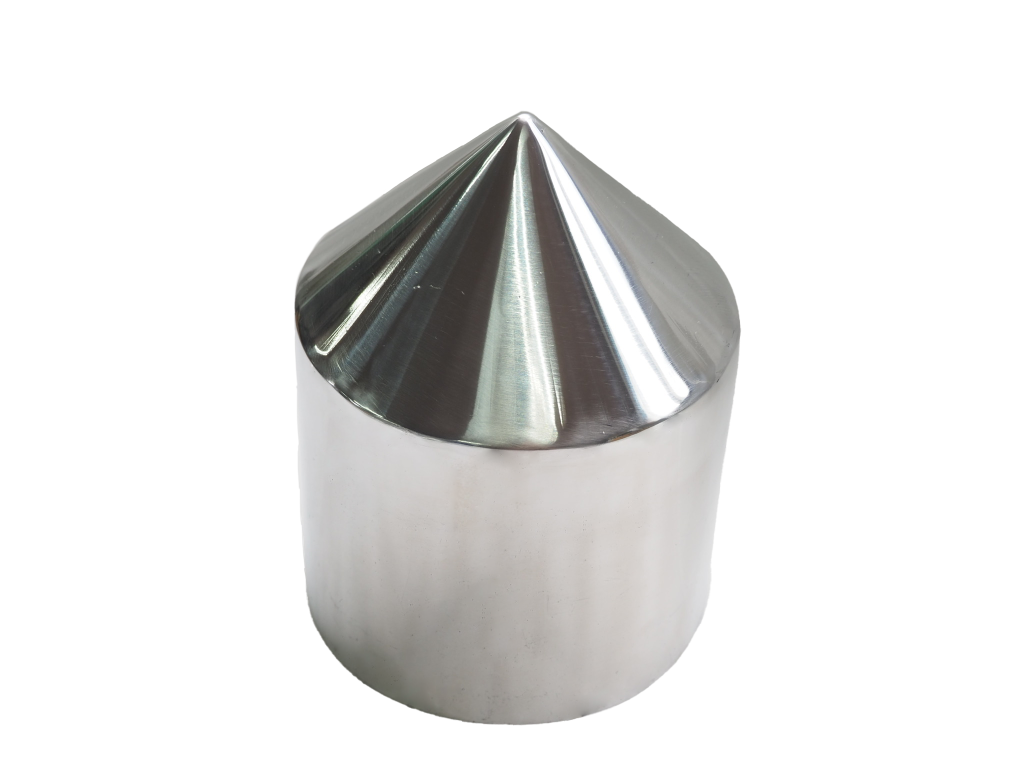
材質 | アルミ |
板厚 | t=2 |
サイズ | φ123 × 160 (mm) |
ステンレスを加工した製品をご紹介します。
この製品の特徴は、「専用金型を使わず」に、「汎用金型を使った送り曲げ」で、「複雑な円錐形状」を実現したことです。
社内で緻密に設計したCAD・CAMデータを元に、ベンダーで何十回も曲げることで、図面通りの円錐形を実現しました。
通常、何十回も送り曲げ加工をする際には、小さなひずみが蓄積されて、ズレが生じてしまいます。
加工工程で発生するひずみを、経験豊富な職人が微調整し、公差内で仕上げました。
汎用金型では加工が難しい特殊な曲げでも、加工する技術がヤマダにはあります。
プレス用の専用金型の製造には高いイニシャルコストがかかってしまいます。
コスト面の制約で専用金型を作ることができない試作の段階でも、ヤマダの技術力で安価に試作が可能です。
特殊な形状でも、まずはヤマダにご相談ください。
焼けやひずみがほとんどなく、美しい溶接
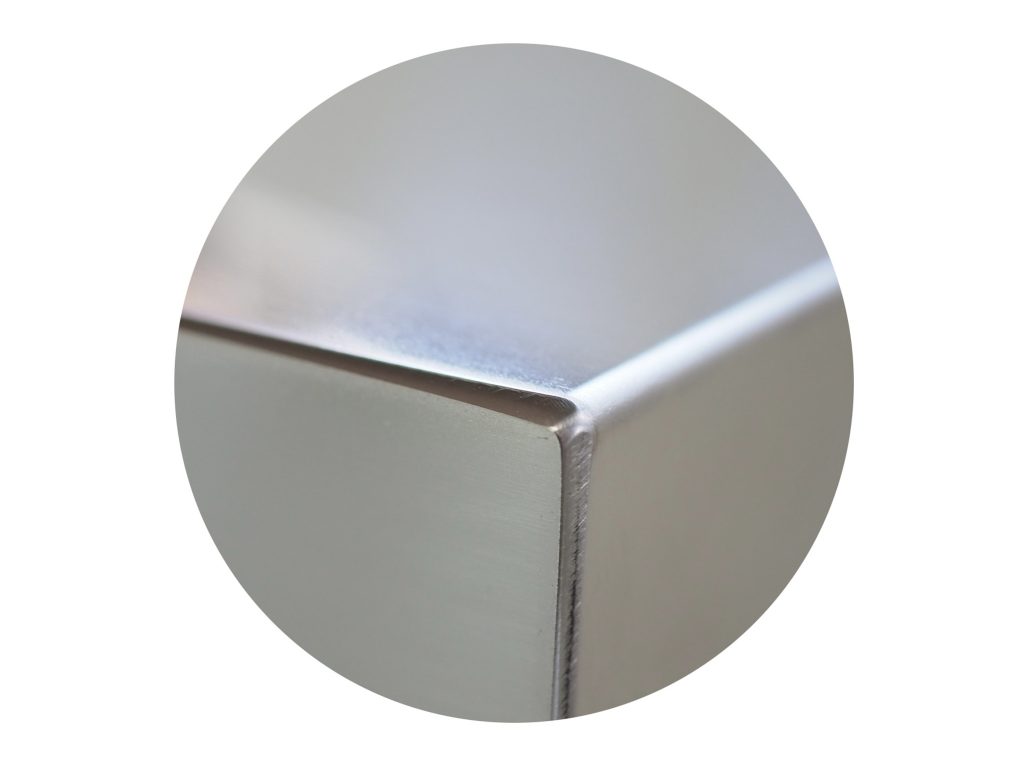
材質 | SUS304 (ステンレス) |
板厚 | t=1 |
最後に、ステンレスを加工した製品をご紹介します。
この製品の特徴は、「高出力のファイバーレーザー溶接機」により「美しい溶接面」を実現したことです。
従来のTIG溶接では、焼け・歪みが大きく、仕上げ工程に時間がかかってしまいます。
この問題を克服するため、ヤマダは、ファーバーレーザー溶接機の導入を早期に決定しました。
当初は300Wのファイバーレーザー溶接機を導入し、お客様から綺麗な仕上がりに満足頂いておりましたが、厚板に対応できなかったのが難点でした。
そこで、定格出力1500Wと高出力で、ステンレス・アルミともに4mmまでの板厚に対応できるアマダ社製「ファイバーレーザ溶接機FLW-1500MT」を導入しました。
これにより、焼けが少なく、低ひずみで、ステンレスの溶接も短時間で綺麗に仕上げることができています。
ヤマダは、薄板はもちろん、厚板の溶接も得意です。
美しい溶接をお求めでしたら、ファイバーレーザー溶接機を導入しているヤマダにお任せください。